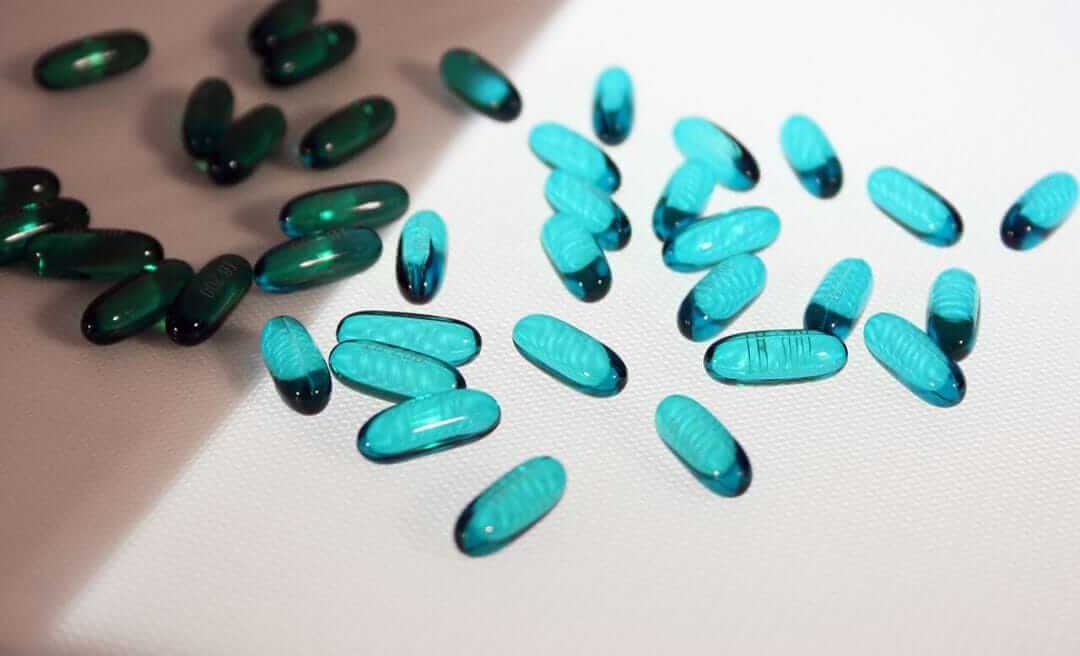
Prioritizing product quality is essential for companies to ensure consumer safety, meet government regulations, avoid costly recalls, and build trust.
Manufacturers must implement thorough inspection processes, and automating these procedures with conveyors can transform your quality control measures.
Why Maintaining High Quality Standards is Critical Across Industries
Strict quality standards are crucial across manufacturing sectors, but this is especially true in highly regulated industries such as pharmaceuticals, food processing, and cosmetics. By upholding high quality standards, your company will:
Avoid Recalls
When defective products make it to market, massive recalls often follow. In the food industry, for example, heightened inspection can help detect contaminants, spoilage, or other defects, thus helping to maintain product quality and preventing meat and produce recalls that damage consumer trust.
High standards, coupled with thorough inspection processes, reduce recall risk and associated costs.
Protect Consumers
Consumers rely on quality standards to remain safe. From spoiled food to damaged blister packs, faulty products can have serious health consequences for consumers. High standards reduce the number of safety issues like spoiled food, damaged packaging, or defective electronics that could harm consumers.
Integrating inspection and testing at key points of your manufacturing process allows you to catch issues before products reach end-consumers and maintain consistent high quality standards.
Meet Legal Regulations
In a number of industries, manufacturers must adhere to strict safety and quality guidelines. Meeting these regulations is mandatory, and implementing thorough product inspections ensures that your products hit the mark.
Competitive Advantages of Automating Your Product Inspection Process
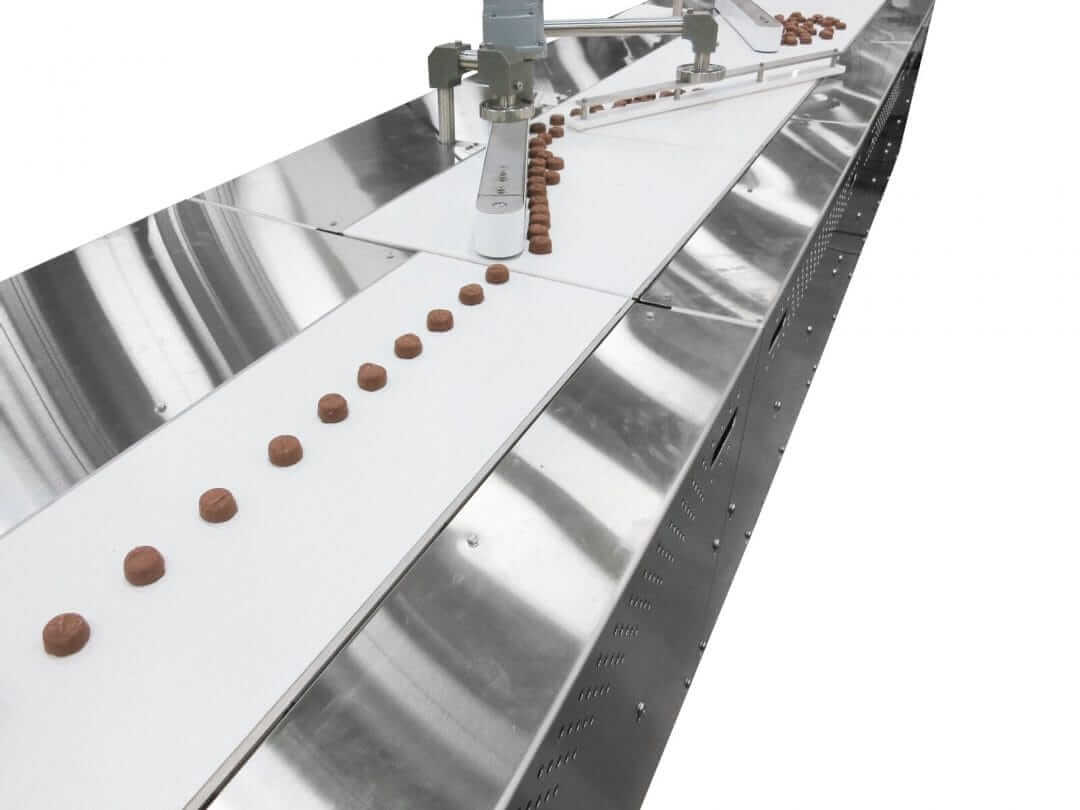
Manually inspecting products is a time-consumer and error-prone process. By automating some elements of product inspection, you’ll gain the following benefits:
Prevent Waste
Automating product inspection can help minimize wasted materials and resources by improving the process of identifying defects and isolating flawed products. You’ll reduce the risk of human error that could otherwise result in faulty products reaching end-consumers or products being mistakenly identified as damaged, expired, or contaminated.
Increase Efficiency
Efficiency improves when your inspection process isn’t a bottleneck. With conveyor systems, you’ll be able to move, sort, and inspect products more quickly and with minimal errors, increasing your efficiency and overall productivity.
Automation also increases throughput, freeing your staff for more strategic tasks.
Reduce Unnecessary Costs
Recalls are costly. Catching product defects through automated inspection before finished goods make it to market eliminates many unnecessary costs associated with recalls, returns, replacements and loss of future sales.
Support Brand Reputation
Upholding high quality standards and minimizing the risk of contamination, defective packaging, and other quality control issues builds brand trust and loyalty. With automation, you can also integrate traceability features into your operation, increasing your ability to track and identify potential issues early.
Gain a Competitive Edge
Leading companies leverage automation to implement higher quality standards and more rigorous inspection processes than competitors. This practice results in better products, more consistency, and increased trust among consumers.
Product Inspection Technology From Dorner: Enhance Your Quality Control Processes
With custom integrated conveyor systems from Dorner, you can improve your product inspection process no matter what industry you’re in.
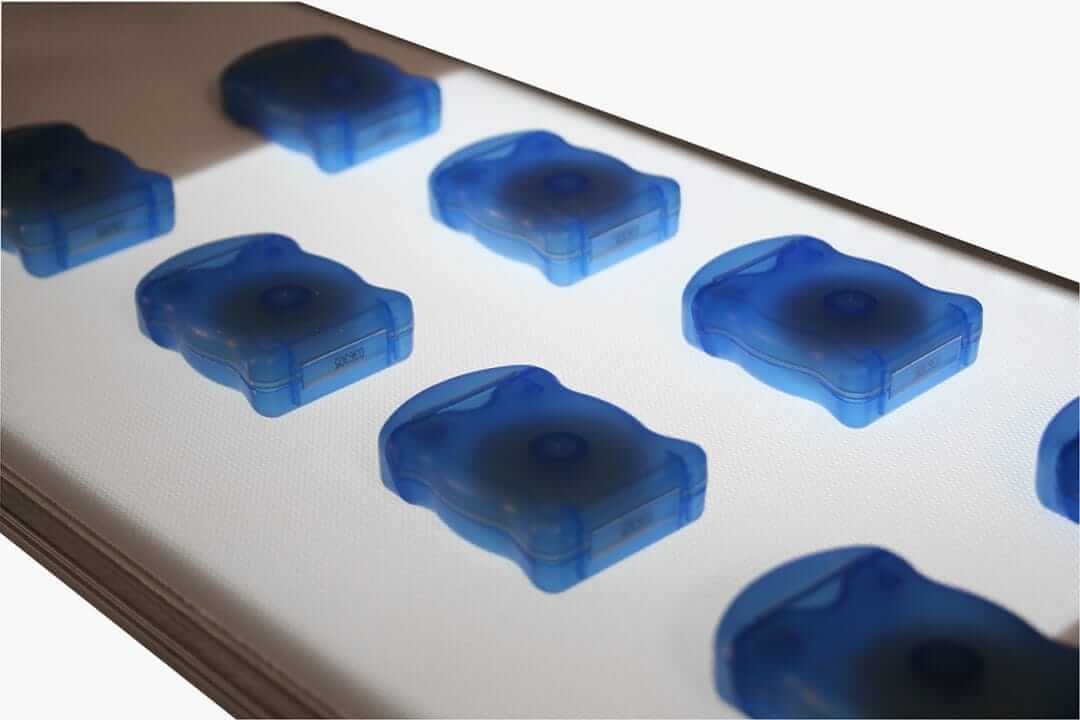
Backlit Industrial & Sanitary Conveyors
Conduct more detailed inspections with backlit conveyor belts. Dorner’s backlit conveyors illuminate products from below, allowing manual and automated vision systems to better detect defects. We offer backlit conveyor sections on our 1100, 2200, 3200, and AquaGard series.
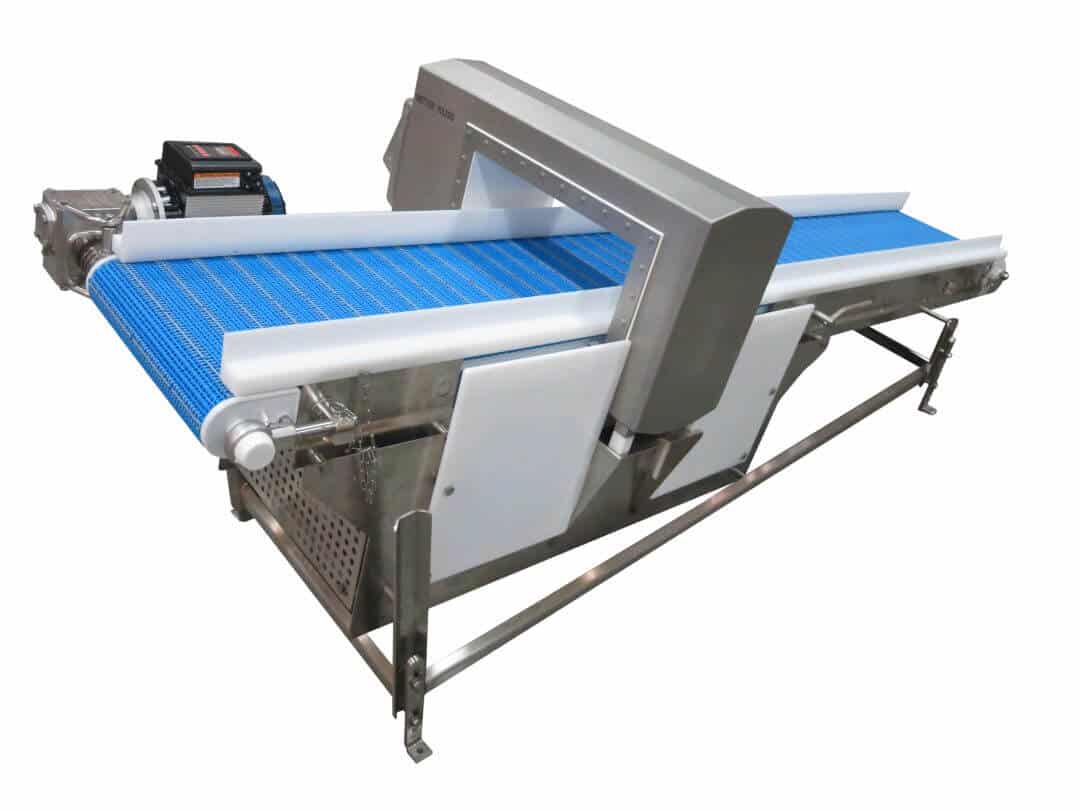
Metal Detection Conveyors
In food processing and pharmaceutical manufacturing, ensuring product quality and consumer safety is key. Dorner offers metal free zone conveyors that, when integrated with metal detectors on your production line, can ensure your products are safe and free of contaminants in an efficient, reliable way.
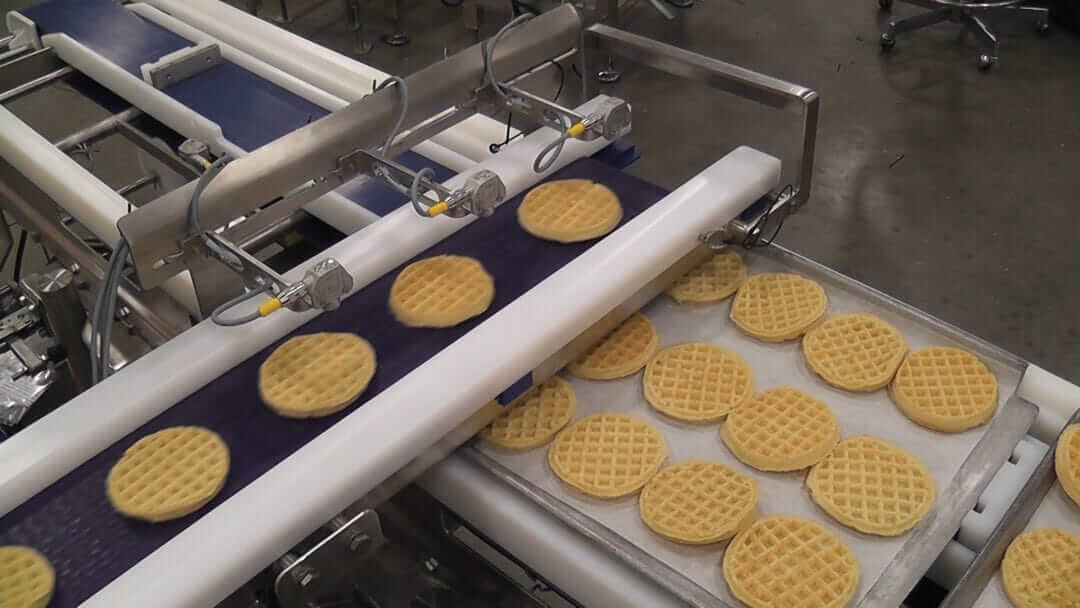
Rejection and Depositing Conveyors
Inevitably, some products on your line will not be fit for distribution. Through product inspection, you’ll be able to efficiently sort out items that can’t be sold or consumed, improving your overall product quality and keeping consumers safe and happy.
With automated conveyor solutions from Dorner, you can easily separate flawed products into reject conveyor accumulators (bins or other conveyors) with the use of diverters, pushers, and automated retracting tails.
Upgrade Your Product Inspection Process and Improve Your Quality Control With Dorner Conveyors
Backlit Industrial & Sanitary Conveyors
Whether you’re in the pharmaceutical, food processing, or other heavily-regulated industries, ensuring your product inspection process runs smoothly and efficiently should be a top priority. With product inspection conveyor systems from Dorner, you can maximize the quality of your products, reducing the risk of costly recalls and keeping your consumers safe.
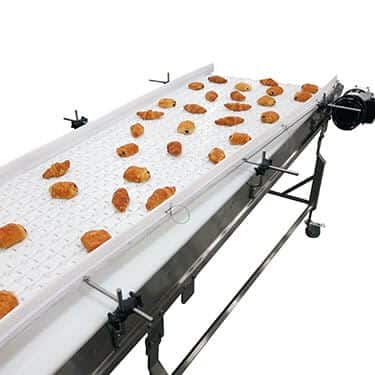